In one of the previous posts, we performed modal analysis and extracted the natural frequencies of the model. If you have not seen that post, you can read about it here. In this post, we will perform a frequency response analysis using Hypermesh.
We will start with understanding what is frequency response, and what leads to these loads and then finally prepare a model and perform the analysis.
What is Frequency Response?
Frequency response as the word states is the study of the response of the body or structure when it is subjected to external frequency inputs which can occur due to environmental conditions. The main thing that we check here is the resonant frequency of the body or structure to figure out the modes of vibration of the structure. You can read more about Modal Analysis here.
Performing Frequency Response Analysis
For this tutorial, we will use a plate, subject it to a certain frequency range, and analyze its behavior.
Meshed Model
In this tutorial, we will be using a plate with 5 holes and mesh with 2D elements, fix the plate with the 4 holes on the periphery, and apply load on the central hole as shown in the image below:
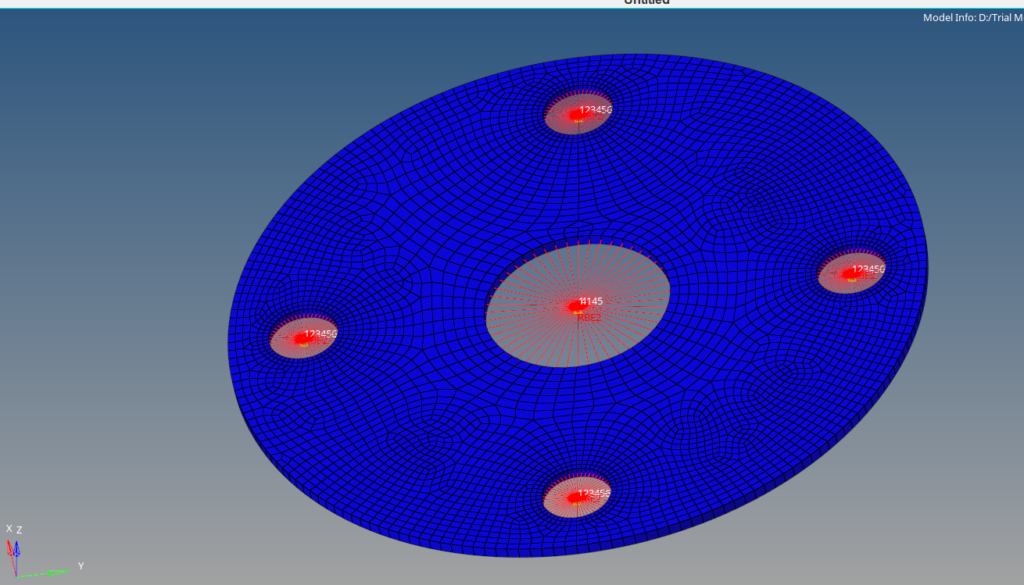
Boundary Conditions
To apply the boundary conditions first we need to create RBE2 elements connecting the nodes on the periphery of the holes to a master node as shown in the image below.
Next, we will constrain the four holes on the periphery of the circular plate. For this we will create a load collector by right-clicking on the white browser area and going to Create -> Load Collectors, we will name this load collector as constraints. We can create the constraints by going to Analysis -> Constraints and selecting the master nodes of the RBE2 elements for those holes.
Now we have to create a DAREA load collector. We can again right-click on the white browser area and go to Create -> Load Collectors, we will name this load collector DAREA. We can create this load collector by going to Analysis -> Constraints and selecting only the dof which is perpendicular to the plate, that is dof2 (y-axis) in this case, we will change the card image of this load collector to DAREA. Select the master node of the central hole to apply this load collector.
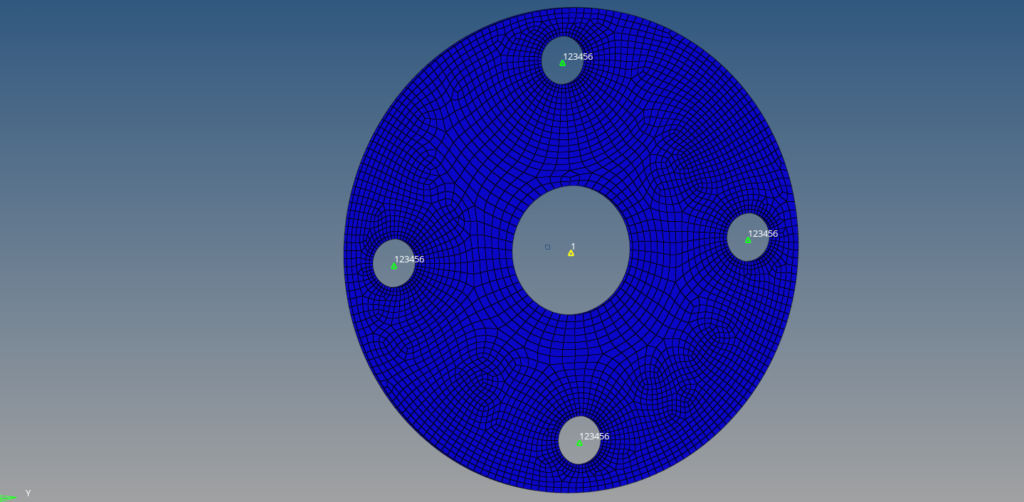
Next, we have to create a TABLED1 load collector. This load collector is created to define the frequency range and the frequency function. We can create the load collector by right-clicking on the white browser area and then going to Create -> Load Collectors, we will name this load collector as TABLED1. Now change the card image of the load collector to TABLED1. Then add two rows under the TABLED1_NUM field. Put the first row as (0,1) and the second row as (1000,1). Keep the XAXIS and YAXIS fields as linear.
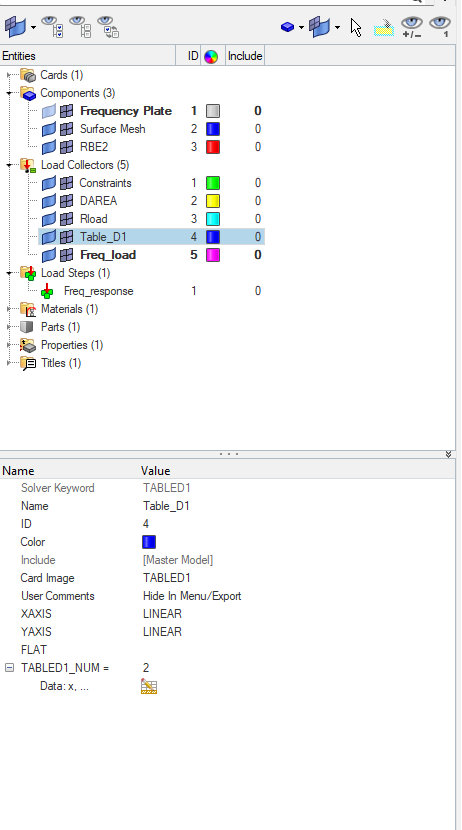
Now we will create a RLOAD load collector. This load collector is used to couple the DAREA and TABLED1 load collectors. We can right-click on the white browser area and then go to Create -> Load Collectors, we will name this load collector as RLOAD. Change the card image of the load collector to RLOAD2. Select the TABLED1 load collector under the TB field and the DAREA load collector under the EXCITEID field.
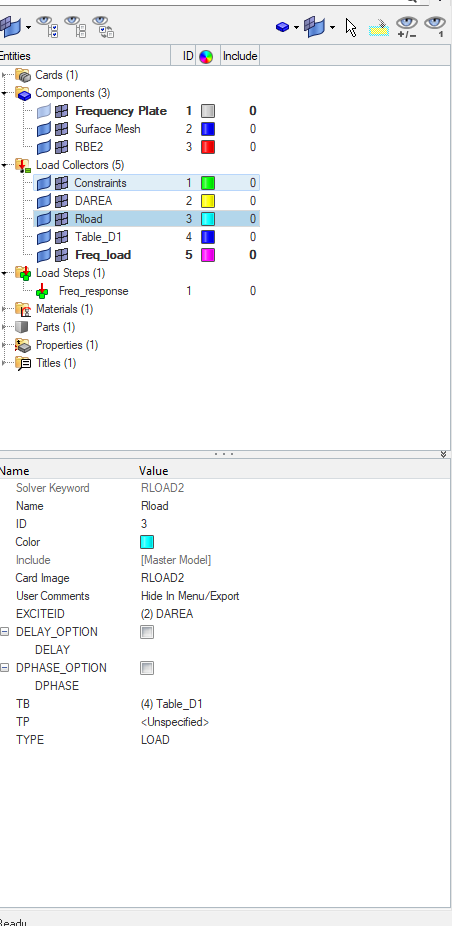
Next, we will have to create a Frequency load collector. This load collector will have the Frequency load. For this, we can again right-click on the browser area and go to Create -> Load Collectors, we will name this load collector as Freq_load. Next, we have to give the starting frequency as 0 under the F1 field, an incremental frequency of 5 under the DF field, and the number of data points as 200 under the NDF field as shown in the image below.

Analysis Setup
We have to now apply material, property, and create load step.
Create a PSHELL property by right-clicking on the white area on the browser area and selecting Create -> Property, then select the card image as PSHELL and assign this property to the plate component. Enter the shell thickness as 2.
Then create a material by right-clicking on the white browser area and going to Create -> Material, we will use steel for this tutorial, the values of steel are available by default in Hypermesh.
Then create a Load step by right-clicking on the white browser area and going to Create -> Load Step. Name the load step as Frequency Response and select the Analysis type as Frequency Response Direct. Select the constraints load collector under the SPC field and the Frequency load collector under the method (struct) field. Once completed the browser area will look very similar to the image below.
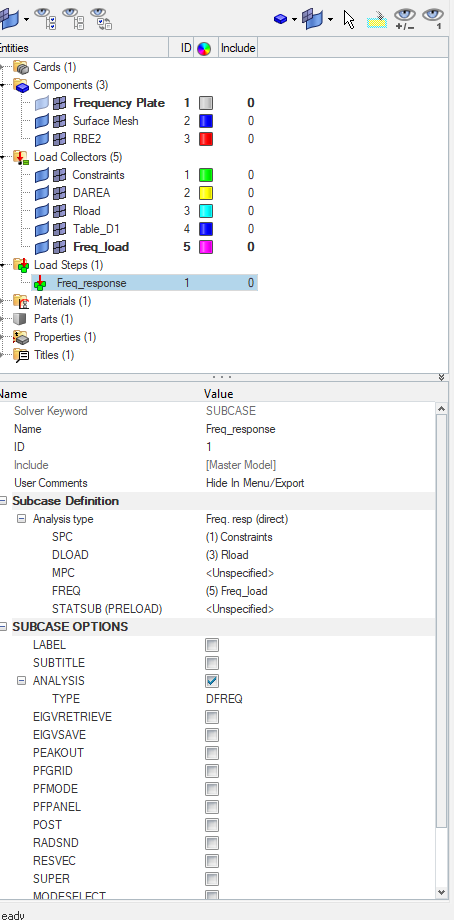
Performing Analysis
First, we will select the output cards required for the analysis. We can do this by going to Analysis -> Control Cards -> Global Output Requests. We will select the Displacement and Stress output cards.
To perform the analysis, we will go to Analysis -> Optistruct, and a window similar to the below image will appear. Kindly note that we are using Optistruct for this tutorial and you can use any other solver of your choice too.
If the optistruct option is not appearing under Analysis in the toolbar. Then go to Preference -> User Profile and select Optistruct. Select export options as custom, run options as Analysis, and keep the memory option as default. Then click on Optistruct to run the analysis. A pop-up window will appear displaying the progress of the run as shown in the below image.
Output
Once the solver run is completed we can view the output values we can also go to View -> Output file as shown in the image below.
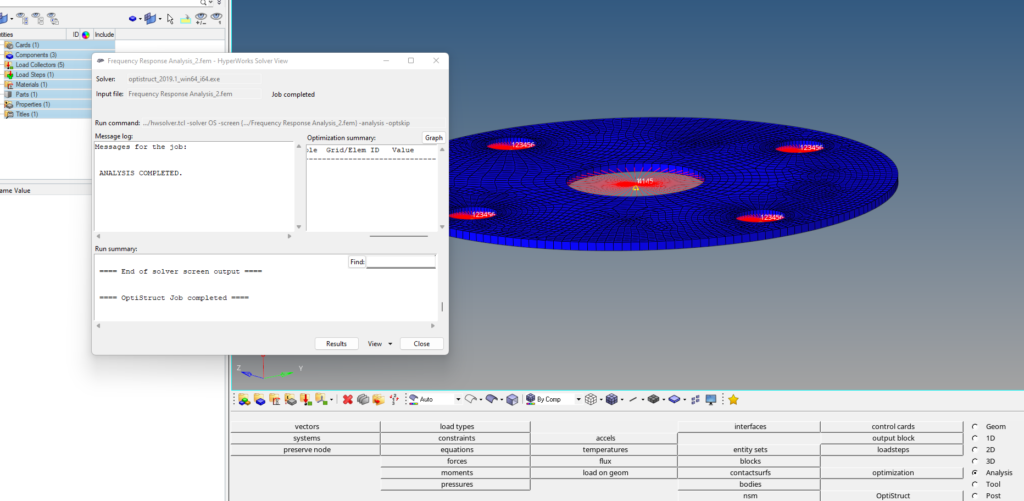
Click on Results to view the results of the Analysis as shown in the image below. A window like the below image image will open. This is the Hyperview window and is used to see the results of the analysis. If you don’t know about this don’t worry I will be making a separate post on this.
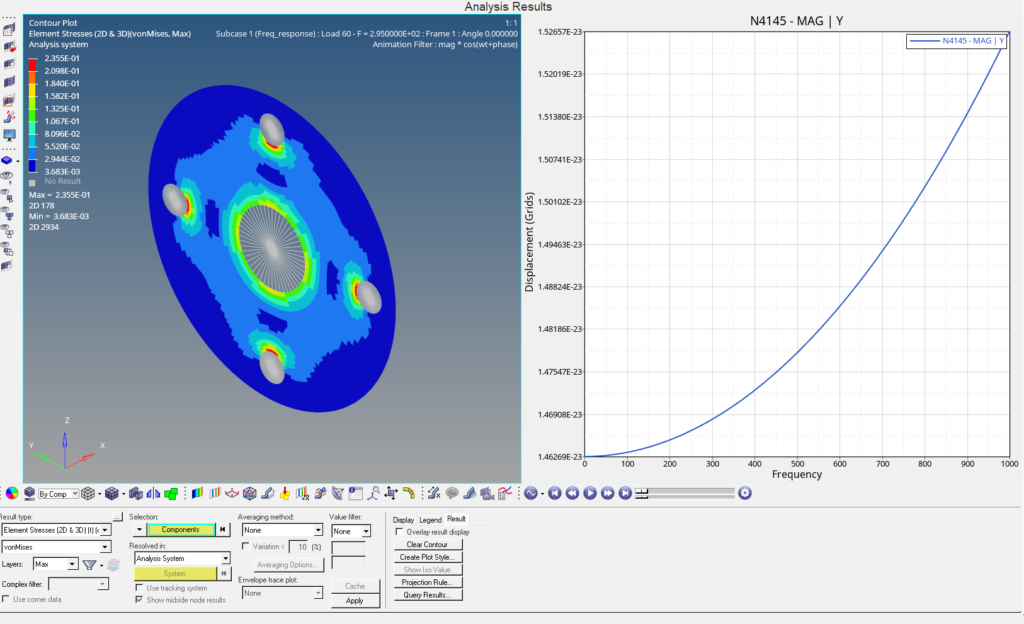
You can also refer to the video below for more clarity on the topic.
This is all for this post see you all in the next post. Don’t forget to follow my Facebook and Instagram Pages. Till then keep learning.